Lithium Battery Pack Factory
Home / Lithium Battery Pack Factory
Quality Assurance
From Component Selection to Final Testing: Ensuring Excellence in Every Step
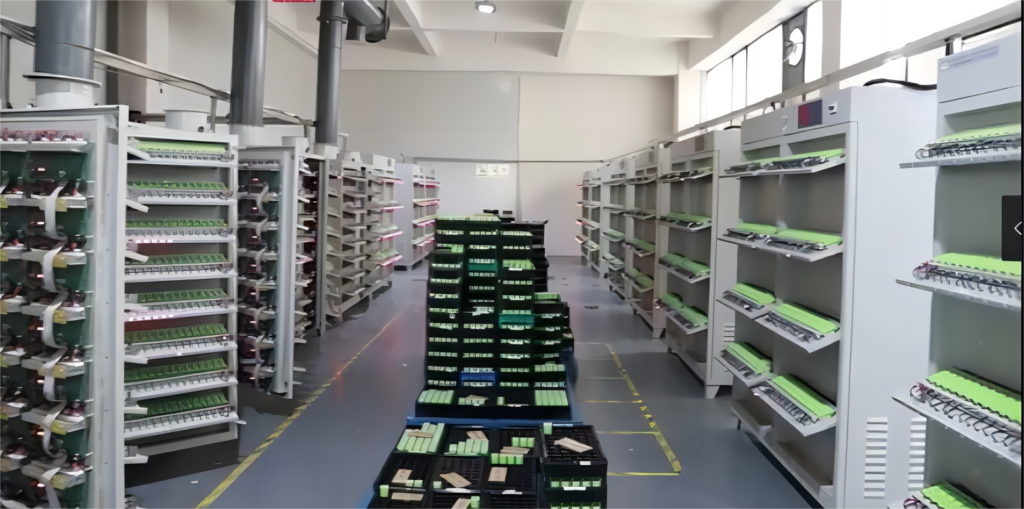
Material Inspection
- Adherence to Standards: Each cell is selected in strict compliance with our “PACK Material Inspection Specification” to maintain consistent quality.
- Impeccable Cell Condition: We ensure that all battery cells are free from stains, scratches, compression, deformation, leakage, rust, damage, or incorrect code spraying.
- Correct Installation: Cells are carefully loaded into the testing fixtures, verifying that the positive and negative terminals are properly aligned.
Detailed Material Selection
At CasiSolar, every cell undergoes thorough sorting and grading based on rigorous criteria. Our specialized data model tracks and evaluates each cell’s performance history, facilitating informed forecasts of its effective service life and ensuring dependable application outcomes.
- Self-Inspection of Cells: We select cells with capacities ranging from 18650 to 2000mAh. Each cylindrical ternary lithium cell must meet the following criteria:
- Capacity: ≥2.0Ah
- Voltage: ≥3.7V
- Resistance: ≤60mΩ
- Environmental Conditions: Temperature at 23±2℃ and Humidity under 50% RH
Grouping Parameters for Cell Consistency:
- Capacity Variation: <20mAh
- Voltage Variation: <30mV
- Resistance Variation: <3mΩ
- Testing Environment: Maintained at a Temperature of 23±2℃ and Humidity less than 50% RH
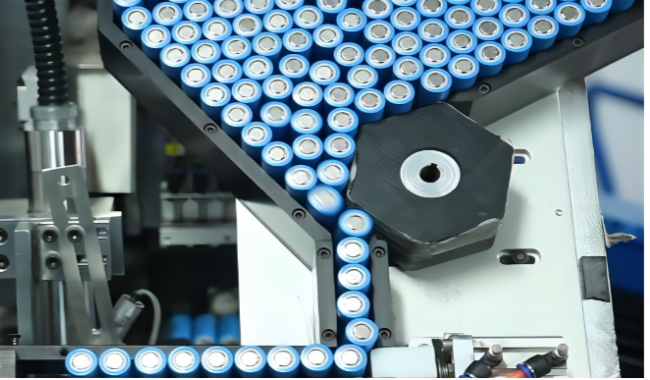
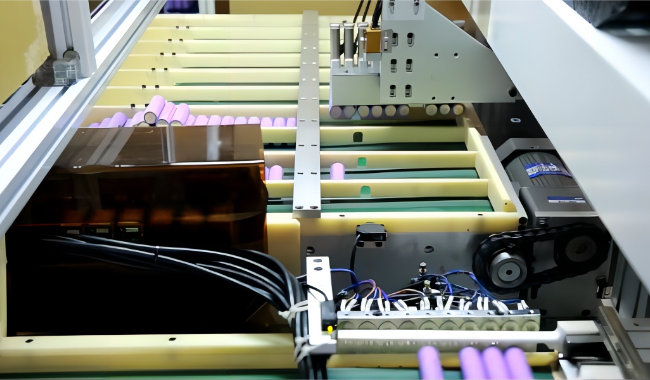
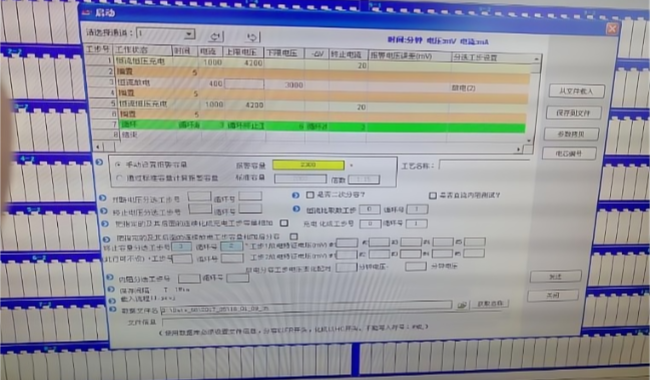
Battery Cell Assembly and Quality Control Procedures
Cell Insertion and Packaging:
- Cell Placement: Insert cells into the lower bracket as specified, cover with the upper bracket, and secure using a rubber hammer.
- Handling Precautions: Operators must wear finger covers to avoid direct contact with the spot welding areas.
- Cleaning Protocol: Avoid immersing cells in industrial alcohol to prevent short circuits.
- Defective Cell Management: Place any defective cells in a yellow turnover box promptly and label them correctly.
- Final Steps: Place the assembled battery pack in a turnover box and affix the appropriate labels.
Spot Welding Module:
- Setup: Install the nickel sheet and battery pack into the mold, then position the mold in the automatic spot welder.
- Programming: Set the spot welder’s program parameters based on the process specifications. Conduct trials with substitute cells to confirm the welding parameters, pressure, and efficacy.
- Welding Tensions: Ensure vertical tension requirements are met:
- Nickel-plated steel belt: ≥4kg (39.2n)
- Pure nickel belt: ≥6kg (58.8n)
- Production Readiness: Switch on the machine, begin welding, and conduct a First Article Inspection (FAI) before commencing mass production.
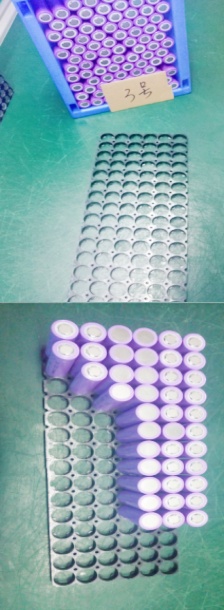
Protection Plate Spot Welding
- Wire Connections: Solder the protection plate pad P+ with a red wire and P- with a black wire.
- Nickel Sheet Welding: Weld the nickel sheet onto the B-, B1, B2, and B+ spots of the protection plate pad. Ensure that each welding spot is clear and secure without any false welds.
- Plate Positioning and Adhesion: Remove the backing of the protection plate’s adhesive and attach it to the battery group. Verify the correct alignment of the protection positions (Protection plate B- aligns with battery B-, Protection plate B+ aligns with battery B+).
- Soldering Quality Control: Ensure the solder is evenly distributed with an ample amount. The soldering iron temperature should be maintained within a range of 360±20°C, with each soldering action not exceeding 3 seconds (ideally 1.5 seconds for best results).
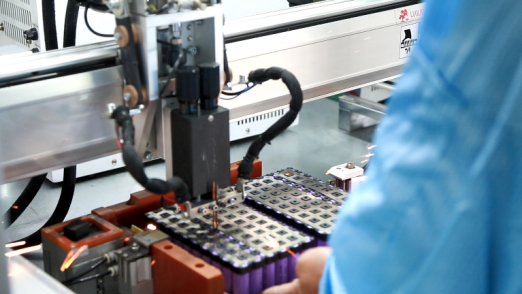
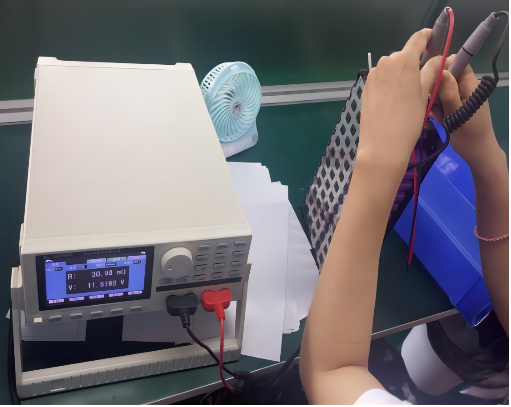
Rework And Quality Control
- Handling Non-Conformance: Identify and rework or repair products that do not meet the quality standards.
- Defect Rate Calculation: Continuously monitor and calculate the defect rate to maintain quality control.
- Minimum Voltage: Ensure the voltage is greater than 11.1V.
- Voltage Consistency: The voltage difference should be 10mV or less.
- Maximum Resistance: The internal resistance must be less than 90mΩ.
- Resistance Uniformity: The resistance difference across the battery should not exceed 50mΩ. (12v60ah for example)
Semi-Finished Product Testing
Setup and Connection:
- Test Cabinet Preparation: Ensure the test cabinet and fixtures are correctly configured and operational.
- Battery Connection: Carefully connect the battery pack to the test cabinet. Attach the red clamp to the positive electrode and the black clamp to the negative electrode, ensuring proper polarity alignment.
- Environmental Settings: (11.1V50AH )
- Temperature: Maintain an inspection temperature of 23 ±2°C.
- Humidity: Ensure humidity levels are kept between 45% and 75% RH.
- Air Pressure: Set the air pressure within the range of 86-106 KPA.
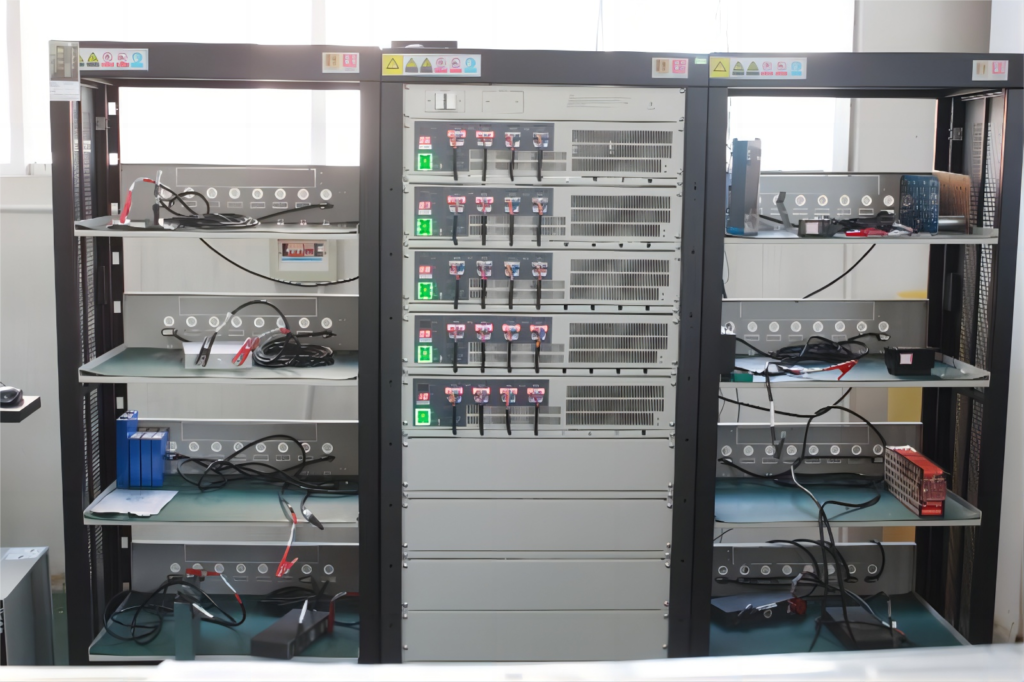
our assembly line
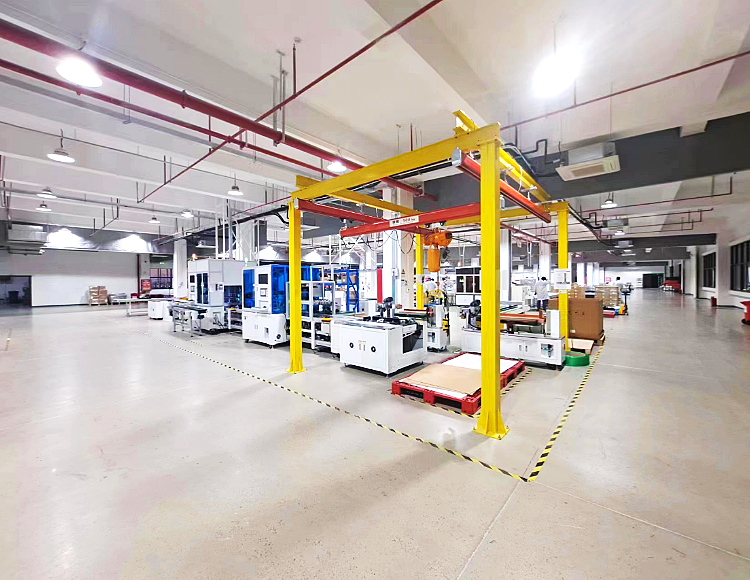
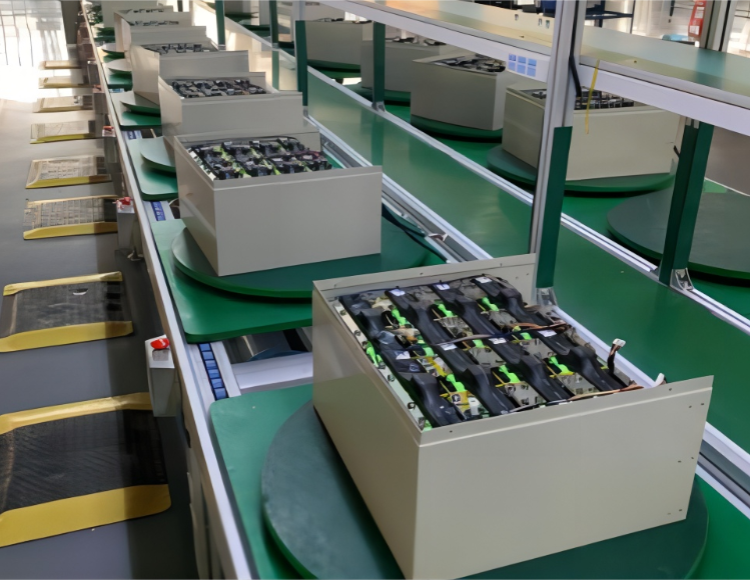
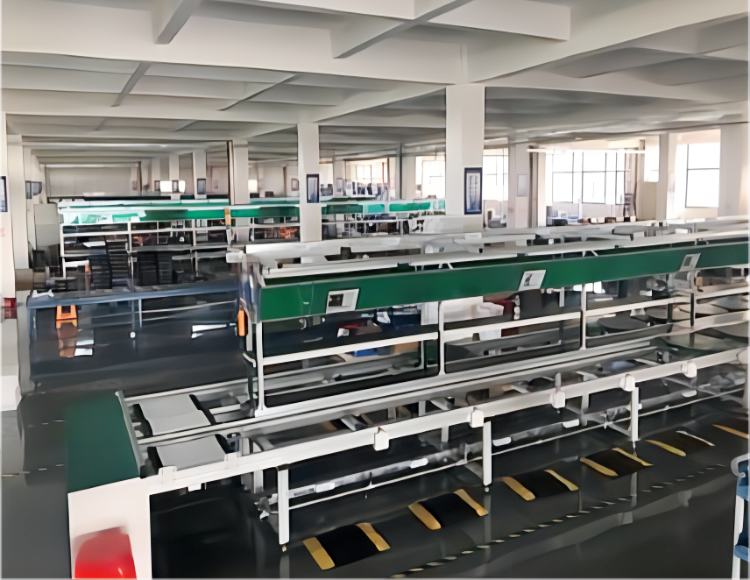
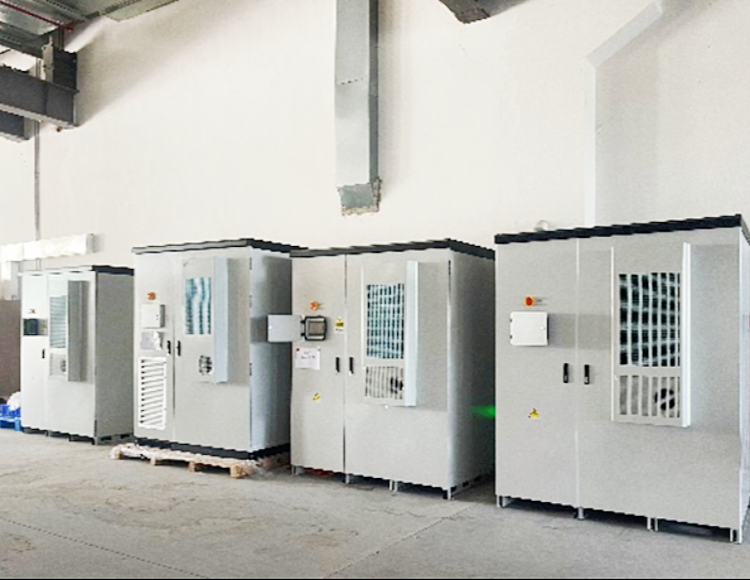
Step 1
Battery Printing
We utilize screen printing to ensure clear, consistent figures, accurate positioning, and the inclusion of the company name and number inside the cover for easy identification.
Step 2
Carton Packing
- Weight Standards: The weight of the surface paper is maintained at 150g/㎡.
- Durability: The case cover can withstand opening and closing at 180° for more than 5 times without damage.
- Integrity: The box remains free from deformation and damage, with a notch crack width of less than 8mm.
- Cleanliness: The surface of the carton is kept clean throughout the packing process.
Step 3
Plywood Packing
For additional protection, we offer plywood packing, which provides sturdy support for the batteries during transportation.
Step 4
Customization Options
Beyond standard packing, we offer neutral packing and the option to print the customer’s brand on the packaging, allowing for further personalization and brand visibility.
Let’s raise your project profit to a new level.
We'd like to work with you
Reach out to CASISOLAR for expert advice and quotes on energy storage solutions. Our team guarantees a response within 24 hours to assist with your specific needs.