AGM Battery Factory
Home / AGM Battery Factory
Durability Redefined
Discover How Our Batteries Outlast Competitors by 2 Years
Raw Material Excellence
At CASISOLAR, our raw material quality control system is pivotal, ensuring our products’ integrity and performance. Key aspects include:
- Material Selection: We prioritize premium materials like Lead ingot: Pb-1, with a purity of ≥99.994%, forming the core of our batteries.
- Material Testing: Rigorous testing, such as the 1-meter drop test for ABS casings, guarantees durability and safety.
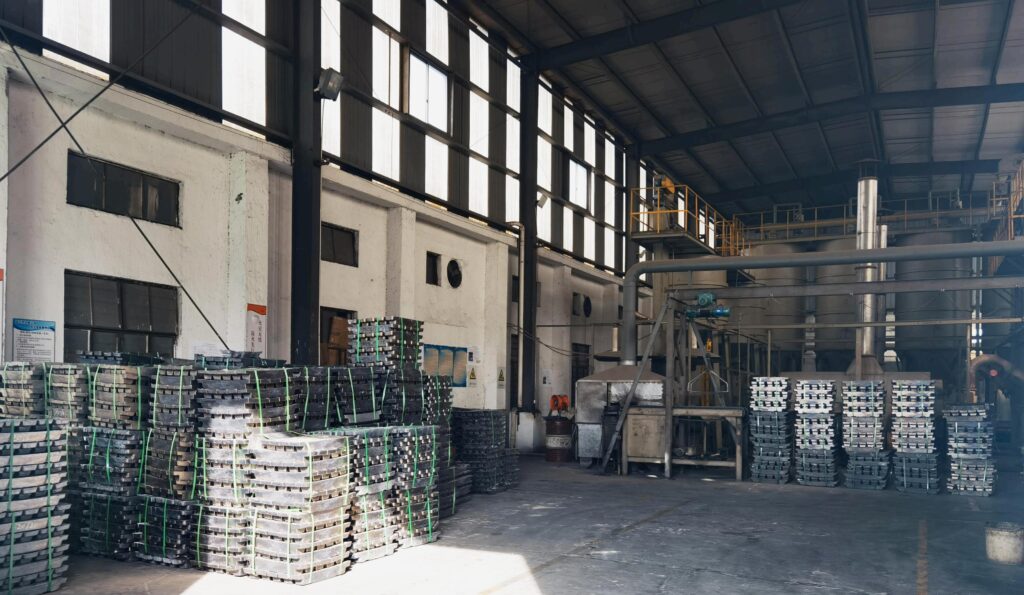
At CASISOLAR, the meticulous production of lead powder marks the first step in our lead-acid battery manufacturing process. This initial stage underscores our commitment to quality, not just in assembly, but in mastering the quality of every component from the ground up.
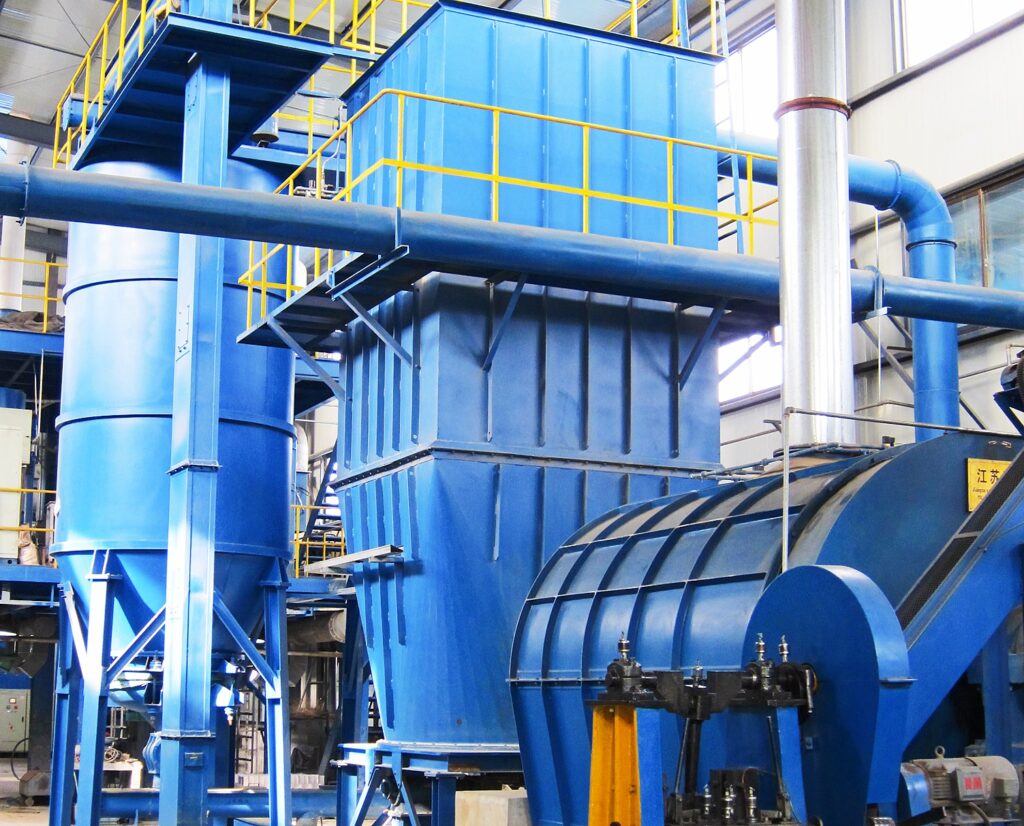
Lead Powder Precision
Our specialized equipment, with its unique powder tanks, ensures the consistency of our lead powder. This careful control is crucial for laying the foundation for the overall performance and reliability of our batteries.
We adhere to strict quality standards for our lead powder:
- Degree of oxidation: 73%-76%
- Apparent density: 1.3 g/cm³ – 1.5 g/cm³
- Regular testing every 3 to 4 hours to ensure compliance
Grid Excellence: The Backbone of Batteries
At CASISOLAR, our grids are crafted from a lead-calcium-tin-aluminum alloy, serving as the foundation for both positive and negative active materials. This choice of alloy ensures low resistance, comparable to that of pure lead, and a high hydrogen evolution overpotential, which minimizes water loss and supports our maintenance-free design.
- Strength and Toughness: Our grids maintain their shape throughout the manufacturing process, preventing deformation.
- Corrosion Resistance: The alloy’s composition provides robust protection against corrosion.
- Hydrogen Evolution Overpotential: High overpotential reduces water loss, enhancing the battery’s longevity.
- Weight and Thickness Standards: We adhere to strict weight standards and maintain a thickness tolerance of less than 0.1mm for the grid and lug to reduce the risk of defects during the welding process.
- Size and Appearance: Our grids are designed to align perfectly without deformation, and we ensure that there are no cracks, holes, or burrs on the frames and ribs, as well as no pinholes or blind spots on the lugs.
Unlike many other factories that outsource their grids, we take pride in producing our own. This allows us to maintain the highest standards of quality and performance for our batteries.
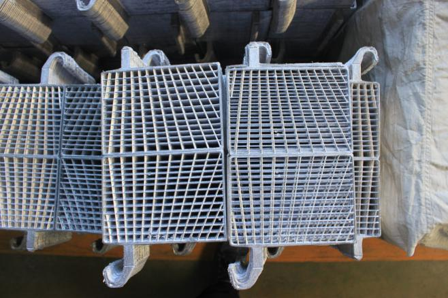
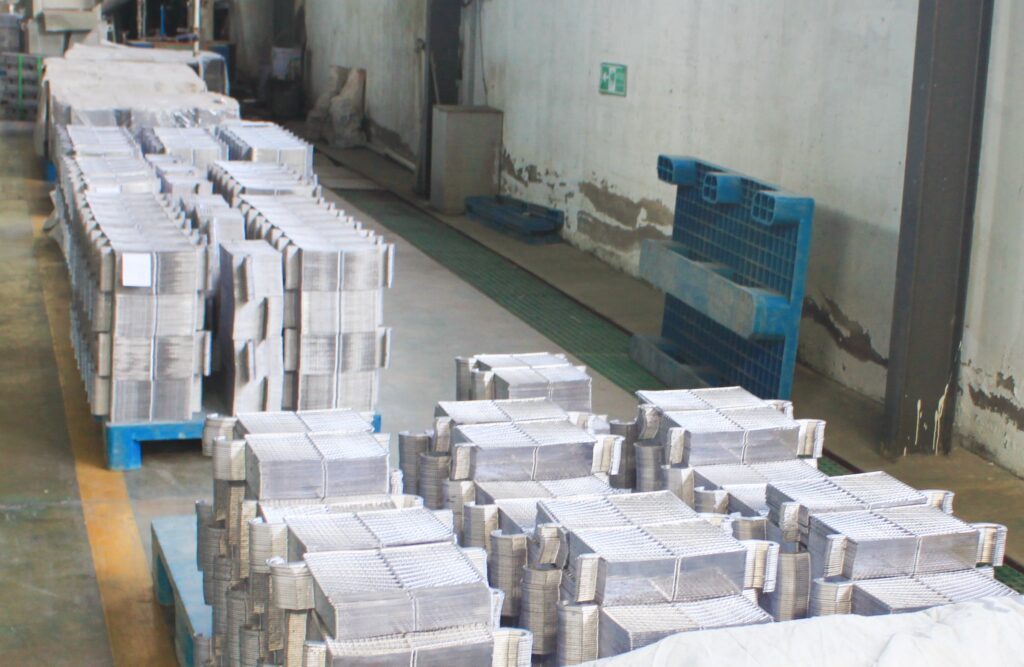
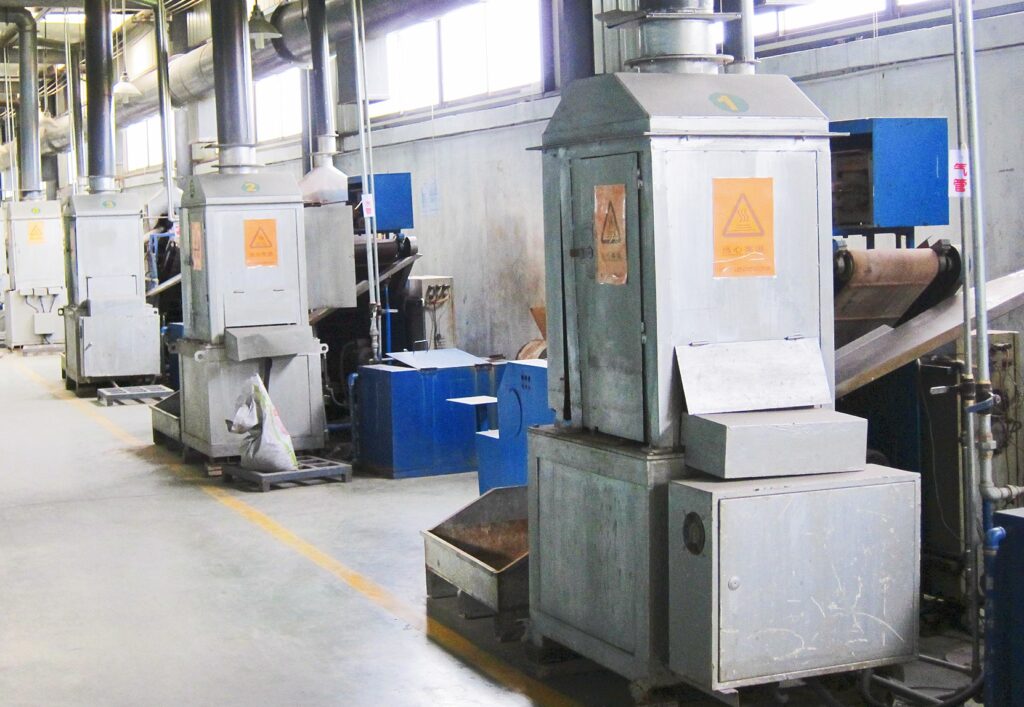
Paste
Paste Preparation:
Quick Water Addition: Ensures minimal oxidation of lead powder to maintain grid strength.
Controlled Acid Addition: Gradual process prevents hardened sulfate formation.
Separate Additives: Negative additives are kept distinct from positive ones to ensure proper battery function.
Apparent Density:
Positive Paste: 4.25-4.35g/cm³
Negative Paste: 4.4-4.5g/cm³
Plate Coating Process:
Weight Consistency: Coated plates are kept within precise weight ranges.
Grid Uniformity: Connected grids are sliced and weighed for consistency.
Stacking Accuracy: 10-grid stacks have a corner height error of ≤1mm.
Acid Trickling Density: Maintained between 1.1g/cm³-1.16g/cm³.
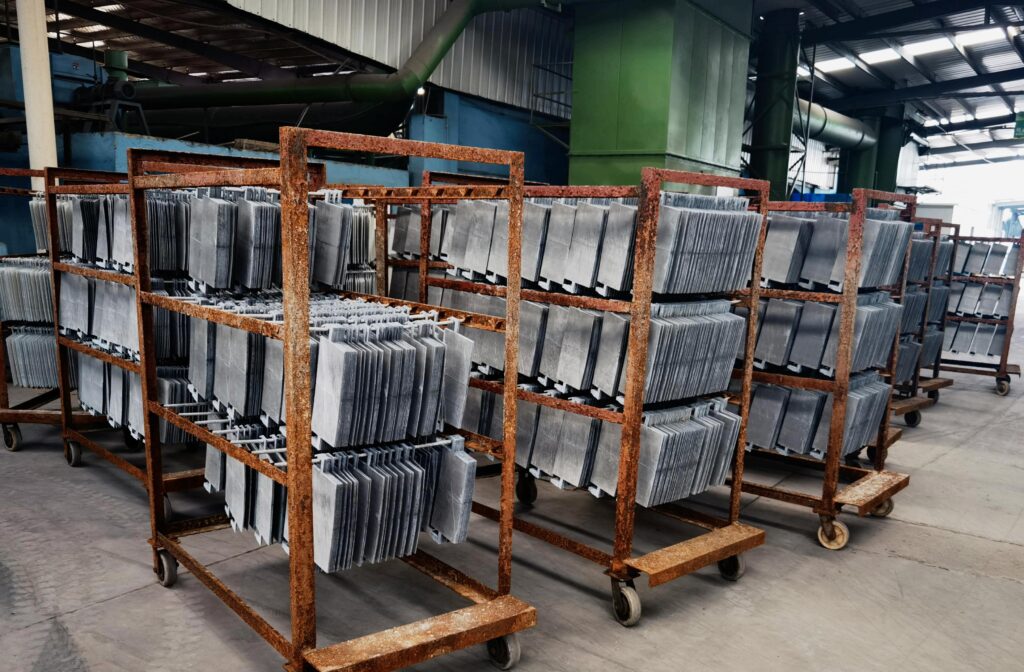
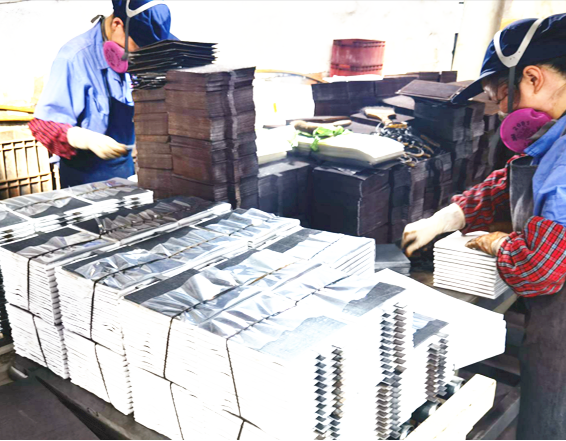
Plates Wrapping and Stacking
Separator is crucial for the overall performance of our batteries. That’s why we use a double-layer AGM separator made of ultra-fine glass fiber, ensuring each plate is wrapped and stacked with the utmost care.
Key Features of Our Separator:
- Consistent Thickness: Our separators maintain a uniform thickness, free from pinholes or mechanical damage, providing reliable insulation between plates.
- Purity: We ensure a low impurity content, contributing to the overall purity and performance of our batteries.
- Durability: With enhanced strength and corrosion resistance, our separators are built to last, supporting the longevity of our batteries.
The meticulous wrapping and stacking process is a testament to our commitment to quality, ensuring each battery is assembled with precision and care.
Welding and Loading
Welding Excellence:
- We use automatic cast-welding with a higher Sn content in the lead strip (1.0%-1.2%), which is three times that of welding, to prevent short circuits and enhance stability.
- Our process eliminates false welding, preventing insufficient battery capacity.
- We ensure no lead slag remains in the pole group after welding, avoiding potential short circuits.
Loading Precision:
- Damaged separators and plates are immediately replaced to prevent capacity issues and short circuits.
- We protect separators and plates from moisture to maintain acid filling and battery capacity.
- Correct polarity is meticulously checked in the battery container to ensure optimal battery performance.
- The assembling pressure is maintained within the range of 1.05Mpa-1.15Mpa, balancing the ease of battery loading and extending battery life.
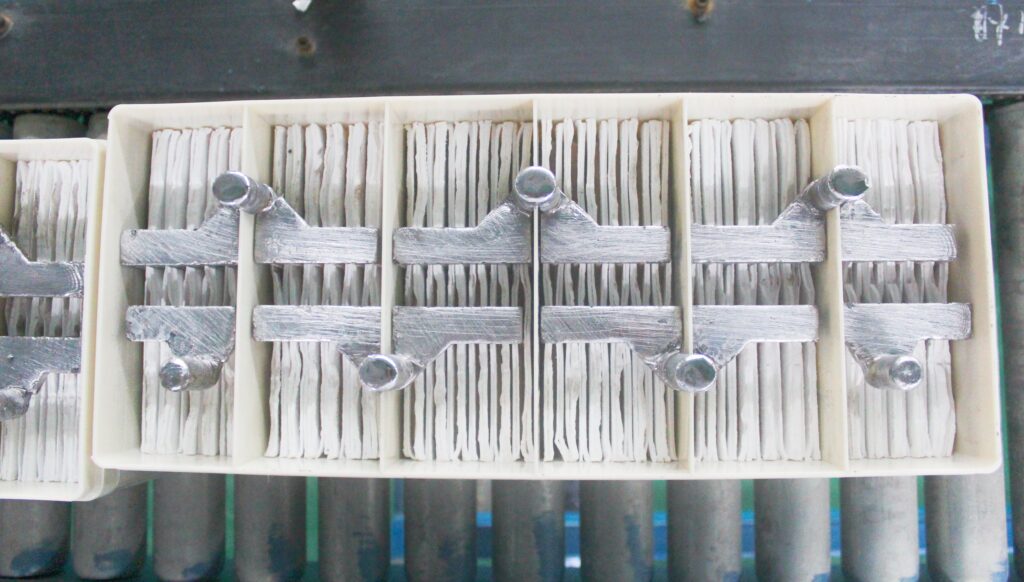
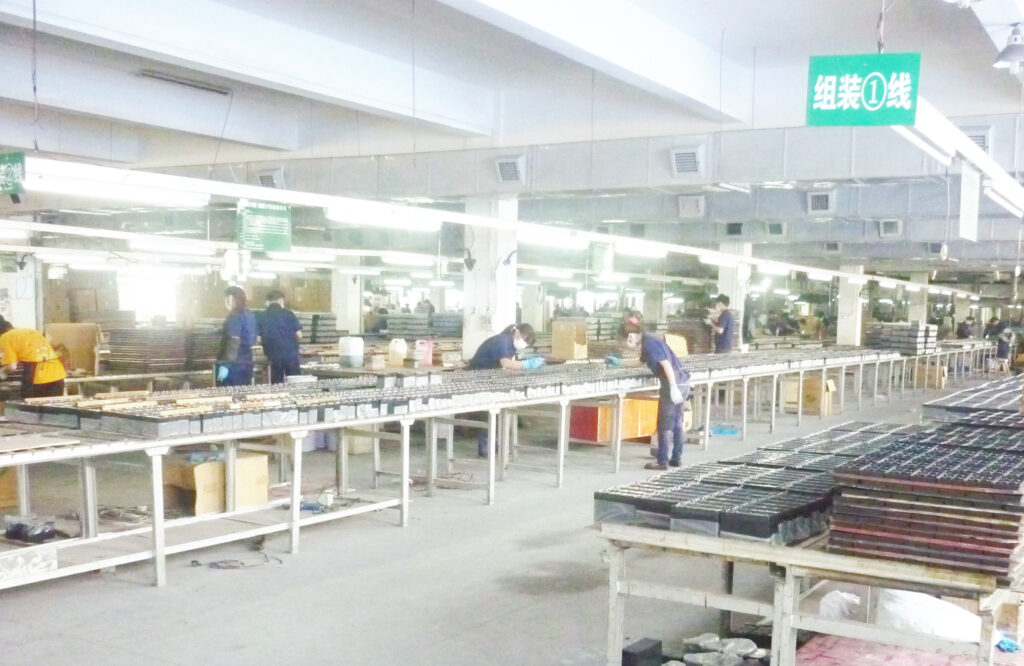
Battery Sealing
Key Principles of Our Sealing Process:
- Compatibility: The main agent and curing agent must be compatible and should never be mixed indiscriminately.
- Proportion: We adhere to a precise ratio of 2:1 for the main agent and curing agent, ensuring optimal sealing efficiency.
- Thorough Mixing: The main agent and curing agent must be thoroughly mixed to guarantee a uniform and effective seal.
Our meticulous approach to battery sealing is a testament to our commitment to delivering batteries that are not only powerful but also durable and reliable.
Welding Output Terminal
Key Features of Our Terminal Welding:
- 360° Welding: We rotate the welding 360° around the pole to prevent false welding, ensuring a strong and reliable connection.
- Post-Welding Correction: After soldering, we meticulously correct the position of the terminal to enhance its appearance and alignment.
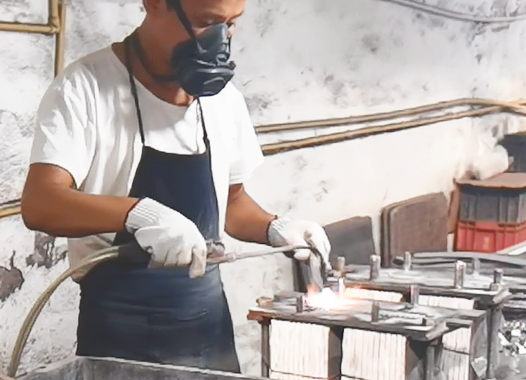
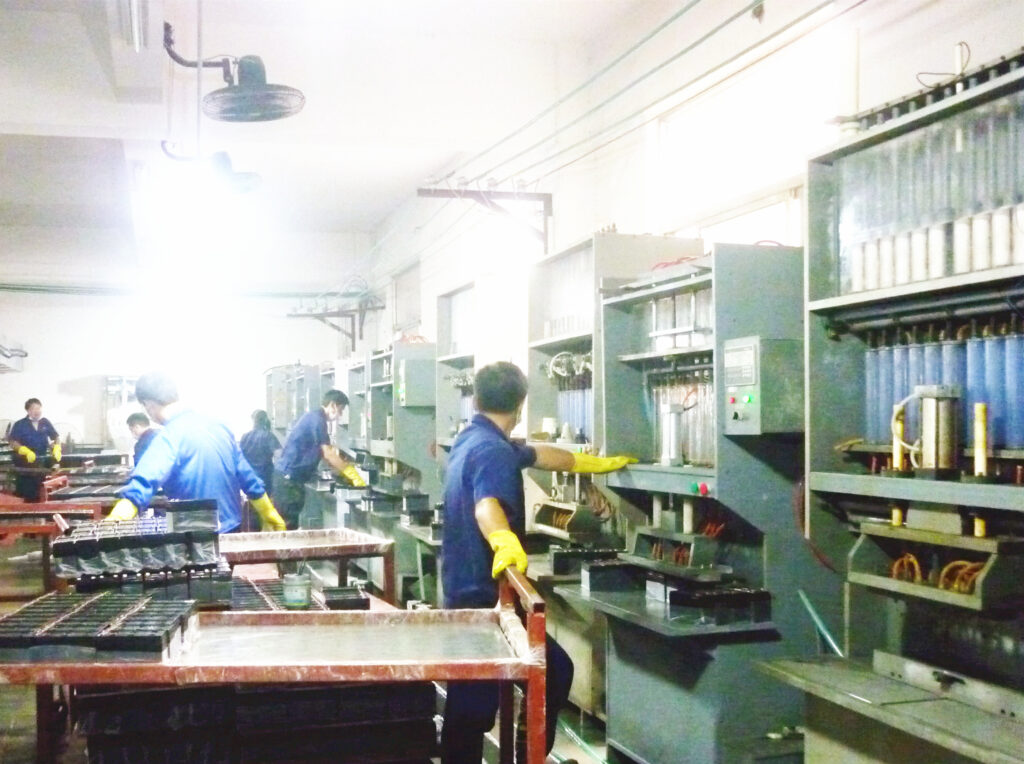
Acid Filling: The Heart of Battery Activation
At CASISOLAR, we produce genuine gel batteries where the electrolyte is gel throughout, from top to bottom. Unlike many other manufacturers that offer “semi-gel” batteries with a layer of gel over lead-acid, our true gel batteries provide superior performance and longevity. We encourage our customers to discern the difference for the best battery experience.
Formation : 5 Charge 4 Discharge Cycles
Why Our Method Stands Out:
- Superior Transformation: Our 5×4 cycle guarantees a complete transformation of active materials, optimizing battery capacity.
- Compared to the Industry: Many manufacturers opt for a 4-charge cycle, and some even limit the process to just 2 charges. Our advanced 5-charge technique offers a distinct advantage, ensuring a deeper, more thorough activation of the battery plates.
Batteries undergo a 24-hour stand test post-cleaning to identify any with unstable voltage, ensuring only the most reliable batteries are delivered to our customers.
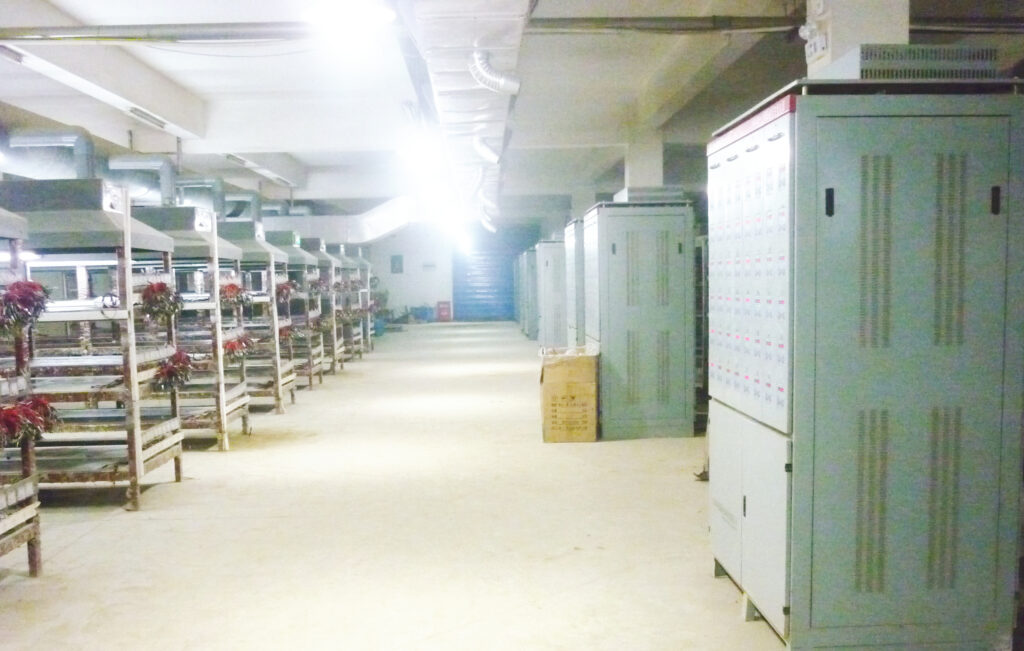
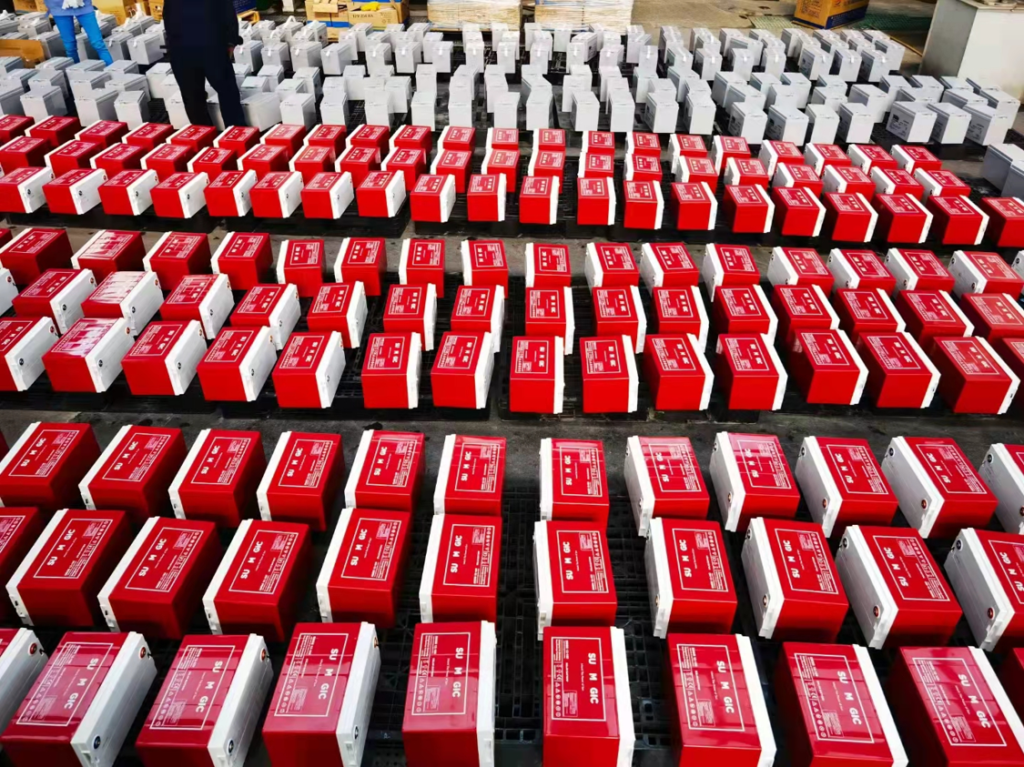
Cleaning & Inspection
- Appearance: We ensure each battery is free from water spots, damage, or deformation, with clear and correct markings for positive and negative terminals.
- Polarity: Batteries are tested for open-circuit voltage, with the positive terminal marked in red and the negative in black.
- Air Tightness: Each battery undergoes horizontal positioning to check for any leakage.
- Weight: We conduct sampling tests for battery weight and maintain records.
- Voltage Testing: We perform open-circuit voltage testing after a 12-hour stand and discharge voltage testing, grouping batteries with similar discharge voltages for consistency.
Battery Grouping: Tailored for Optimal Performance
- Appearance: We ensure each battery is free from water spots, damage, or deformation, with clear and correct markings for positive and negative terminals.
- Polarity: Batteries are tested for open-circuit voltage, with the positive terminal marked in red and the negative in black.
- Air Tightness: Each battery undergoes horizontal positioning to check for any leakage.
- Weight: We conduct sampling tests for battery weight and maintain records.
- Voltage Testing: We perform open-circuit voltage testing after a 12-hour stand and discharge voltage testing, grouping batteries with similar discharge voltages for consistency.
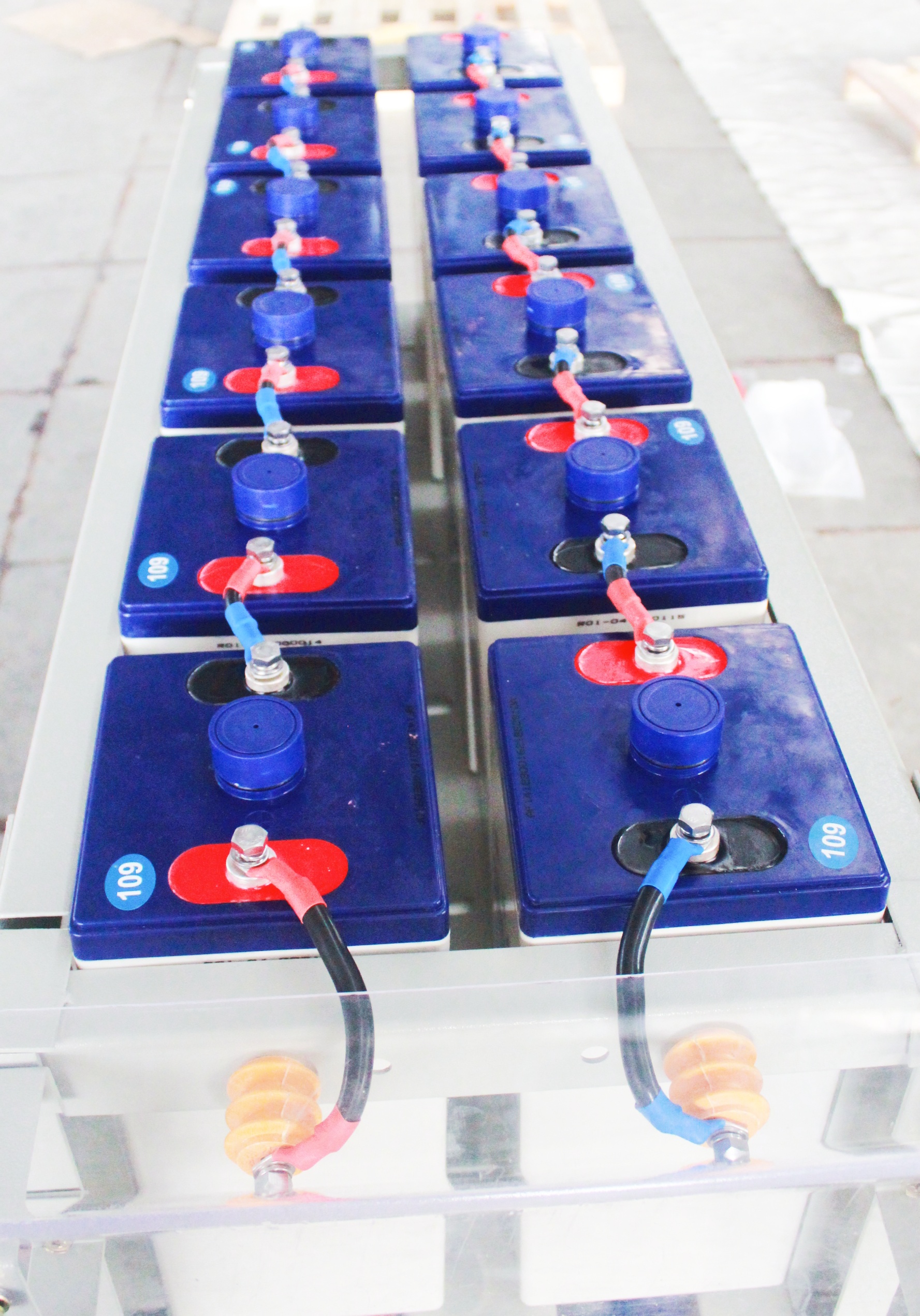
Tests before delivery
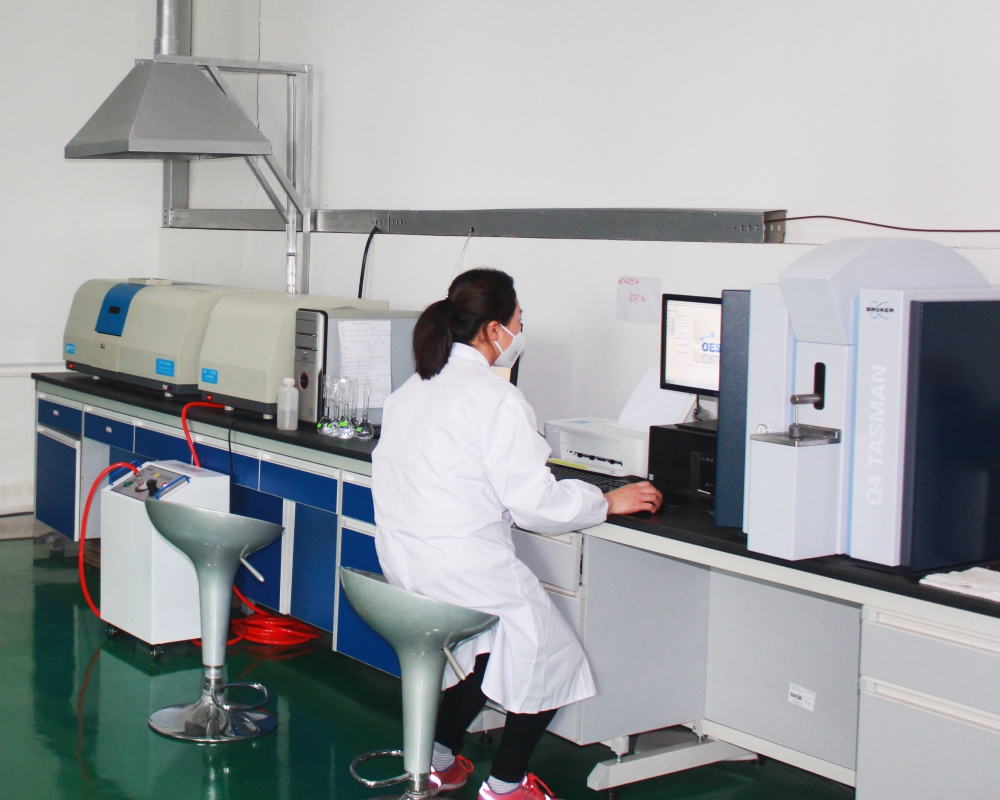
Raw material test
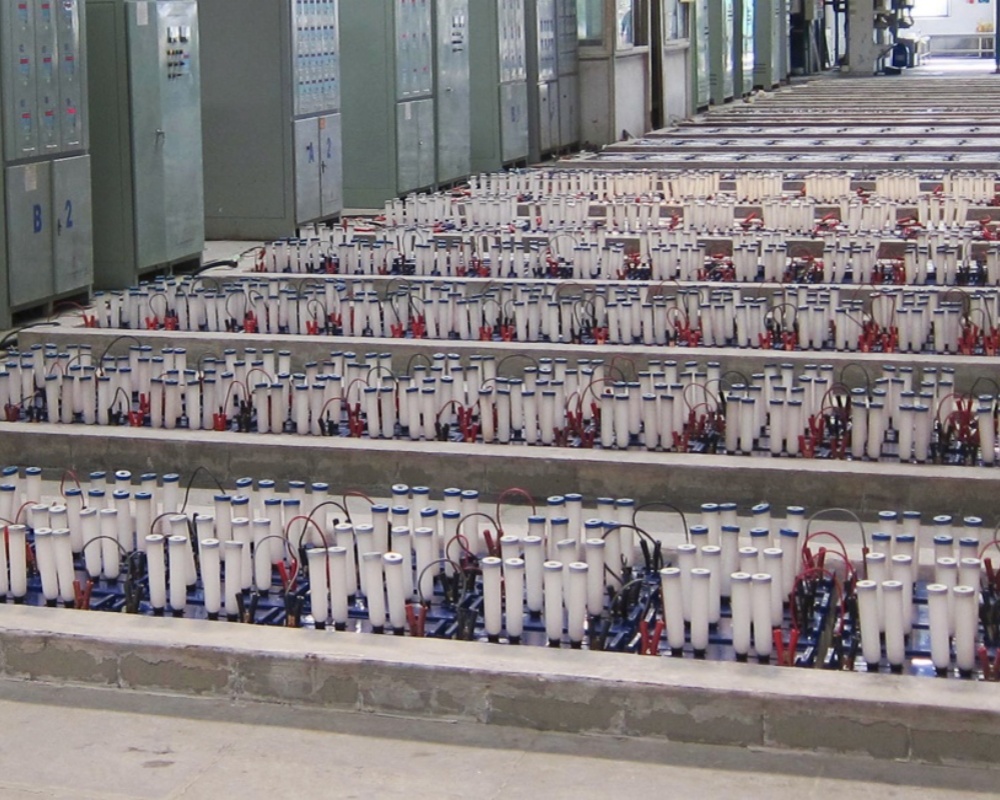
Charge & discharging test
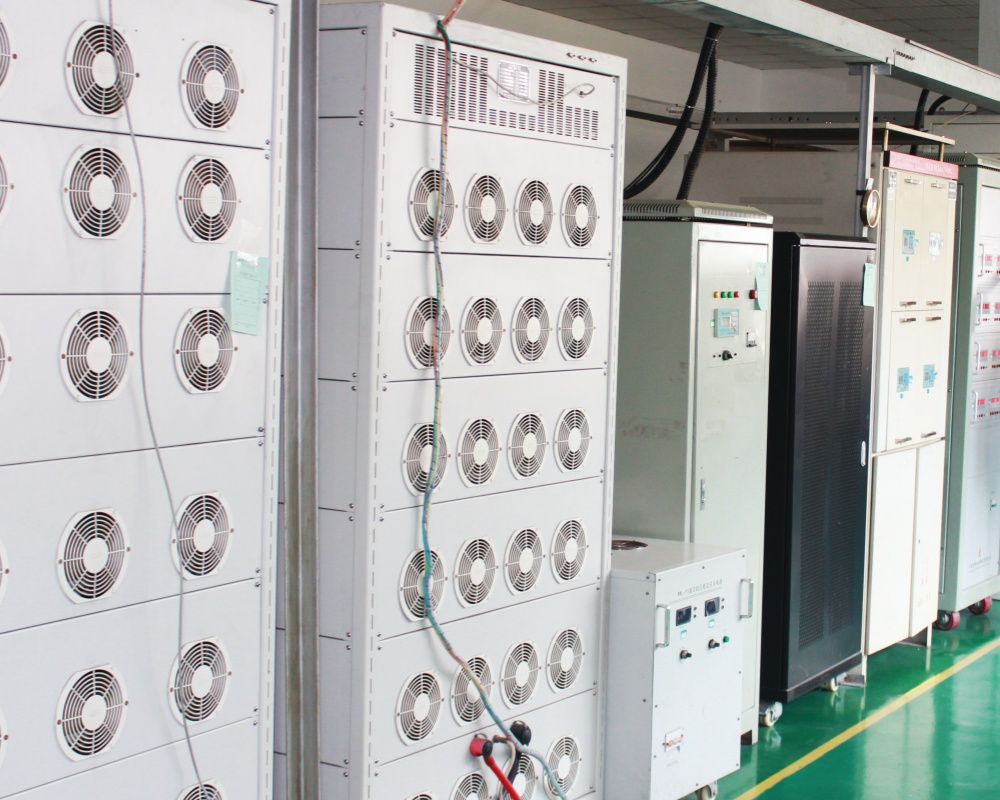
battery performance test
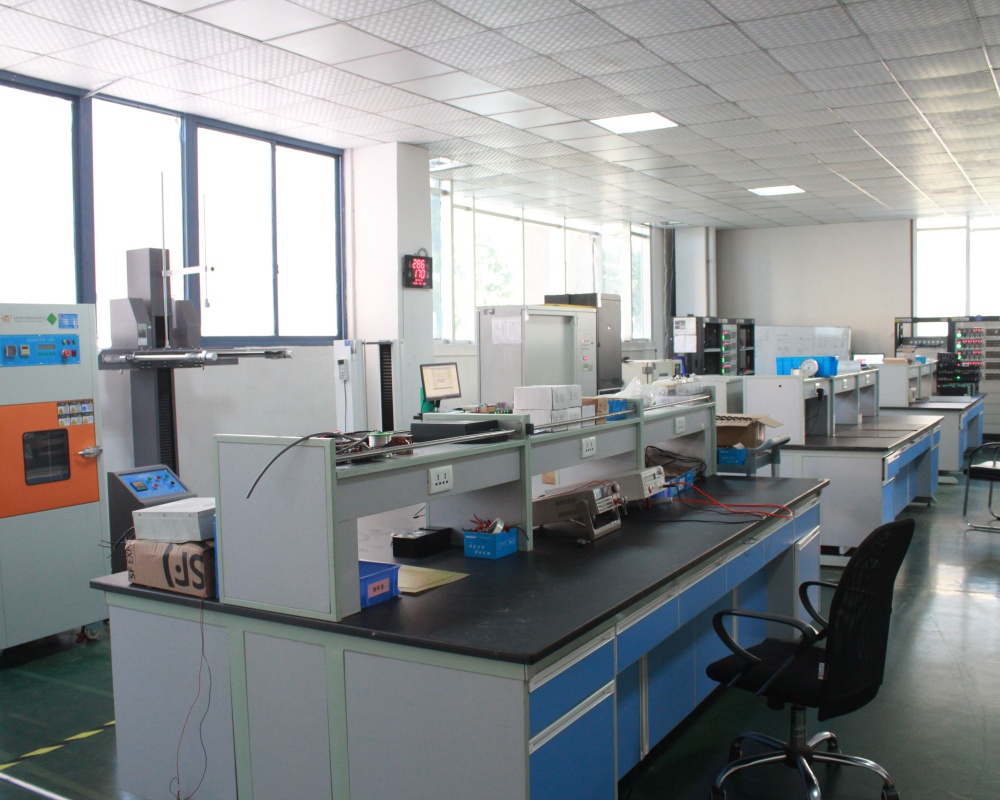
voltage/current/resistence test
Step 1
Battery Printing
We utilize screen printing to ensure clear, consistent figures, accurate positioning, and the inclusion of the company name and number inside the cover for easy identification.
Step 2
Carton Packing
- Weight Standards: The weight of the surface paper is maintained at 150g/㎡.
- Durability: The case cover can withstand opening and closing at 180° for more than 5 times without damage.
- Integrity: The box remains free from deformation and damage, with a notch crack width of less than 8mm.
- Cleanliness: The surface of the carton is kept clean throughout the packing process.
Step 3
Plywood Packing
For additional protection, we offer plywood packing, which provides sturdy support for the batteries during transportation.
Step 4
Customization Options
Beyond standard packing, we offer neutral packing and the option to print the customer’s brand on the packaging, allowing for further personalization and brand visibility.
Let’s raise your project profit to a new level.
We'd like to work with you
Reach out to CASISOLAR for expert advice and quotes on energy storage solutions. Our team guarantees a response within 24 hours to assist with your specific needs.